Keys to a Successful OSHA Annual Review of Your Lab’s Health & Safety Plan
A solid health and safety plan in the lab not only meets regulatory requirements, but also fosters a secure environment for staff
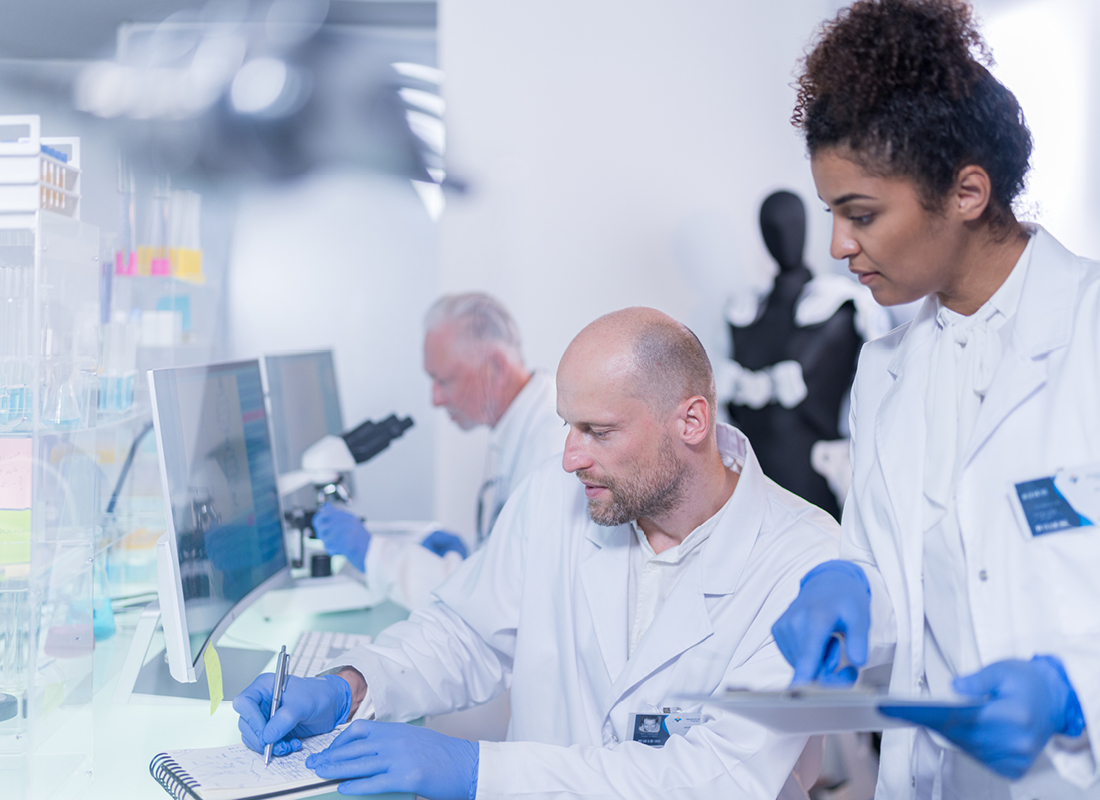
The US Occupational Safety and Health Administration (OSHA) does not provide accreditation for laboratories, but many of the typical lab accrediting agencies create standards for labs based on the OSHA requirements labs must follow. The Joint Commission (TJC), College of American Pathologists (CAP), and COLA are well-known accrediting agencies for clinical laboratories. Each uses audits and checklists to ensure their customer labs remain compliant with OSHA regulations.
As part of these accreditation standards and regulations, laboratory leadership has much to do to ensure the safety program is complete and fully operational. A solid health and safety plan in the laboratory not only meets regulatory requirements, but also fosters a secure environment for employees. Here are the critical components and OSHA standards to consider in a regular review, each of which ensures that the lab demonstrates both its compliance and commitment to staff well-being.
Bloodborne pathogens
Bloodborne pathogens (BBP) are a persistent threat in laboratories where handling of biological materials occurs frequently. The OSHA Bloodborne Pathogens Standard (29 CFR 1910.1030) requires labs to establish and maintain an Exposure Control Plan (ECP). Updating and assessing this plan annually is essential.
Ensure the ECP outlines the latest safety procedures, including the proper handling and disposal of sharps, the use of engineering controls like safety needles, and the use of personal protective equipment (PPE). Review and reinforce the use of safe work practices and engineering controls that prevent exposure to bloodborne pathogens, such as handwashing and using sharps containers and biological safety cabinets. Revisit laboratory cleaning procedures and verify that lab surfaces and equipment are properly decontaminated after exposure incidents. Lastly, ensure all staff have completed annual training on handling bloodborne pathogens, spill response, and sharps safety. Training records should show all employees are up to date.
Chemical management
OSHA’s Hazard Communication standard requires labs to have an accurate and comprehensive inventory of all chemicals used. Labs must also have Safety Data Sheets (SDS) accessible for each chemical. This is not only for regulatory compliance, but also to safeguard staff from chemical hazards. In addition, the OSHA Lab Standard (29 CFR 1910.1450) mandates a Chemical Hygiene Plan (CHP) to address chemical use in labs. The CHP should reduce exposure to hazardous chemicals and outline safety protocols, emergency response procedures, and specific precautions.
To establish and review the lab’s chemical inventory, confirm all chemicals in the lab are documented, including their quantities and storage locations. Update the list to reflect new chemicals and discard expired or unused ones. Verify that Safety Data Sheets (SDSs) are accessible for all chemicals. Digital access is common, but labs should ensure SDSs are organized for quick reference in an emergency. A backup to an electronic system is also required. Check that all chemical containers are labeled with the chemical identity, hazard warnings, and the expiration date. Chemicals should be stored based on compatibility (do not store in alphabetical order), and flammable materials should be housed in designated cabinets. Ensure spill kits are well-stocked, and that staff are trained in their use. Each lab area should have a response plan in place for different types of spills, with clear procedures and defined responsibilities.
The laboratory’s Chemical Hygiene Plan should be current, reflecting changes in chemical processes or safety procedures over the past year. Evaluate whether employees are following CHP guidelines, and make necessary adjustments based on feedback and incident reports. Check for consistency in safety practices—such as PPE use and adherence to standard operating procedures (SOPs)—as indicators of the plan’s effectiveness. Conduct routine safety audits to identify weaknesses in the current CHP and ensure corrective actions are in place.
Injuries and exposures
Analyzing injury and exposure incidents is crucial for identifying trends, addressing root causes, and preventing future accidents. This proactive approach aligns with OSHA’s goals of proper injury reporting and maintaining a safe workplace.
Confirm that all reportable injuries and exposures are accurately logged and reviewed. This includes assessing injury frequency and types to identify any patterns that might require a safety protocol update. For each recorded incident, analyze the cause to determine if it was preventable. Identifying factors like inadequate PPE, poorly followed protocols, or training gaps can lead to more effective mitigation strategies. Ensure incidents are promptly evaluated to implement preventive actions, update protocols, and schedule any necessary re-training. It is best to encourage open dialog, so employees feel comfortable reporting “near misses” or minor incidents. These can provide valuable insights into potential hazards that haven’t yet led to serious injuries.
Employee training
In each OSHA safety standard—Bloodborne Pathogens, Hazard Communication, etc.—there is a section mandating proper employee training surrounding the topic. Laboratories need to provide regular training on a variety of safety topics, and properly documented training helps ensure compliance and reinforces the overall culture of safety.
Lab safety training must cover OSHA-required topics such as chemical safety, BBP protocols, PPE usage, and emergency procedures. Training for these topics should occur annually or more frequently as needed. Include drills of specific emergent responses that may be required of staff (i.e. fires, evacuations, disaster response). Be sure every staff member has completed the required training and drills. Missing or outdated records can be red flags should an OSHA inspection occur. Review the lab’s training logs to confirm all sessions are documented with attendee names, dates, topics covered, and trainer credentials. Consider implementing a system that automatically tracks training deadlines to streamline compliance.
Policies and procedures
One last consideration for a review of the lab safety program is a safety policy and procedure review. While accrediting agencies like CAP or TJC require that lab documents are reviewed once every two or three years, OSHA makes a specific requirement for an annual policy review in some of their safety regulations. While conducting the lab’s annual health and safety review, it is best practice to review and update all safety policies and procedures as well.
Takeaway
Completing an annual OSHA review of your lab’s health and safety plan requires a proactive, detailed approach. By focusing on BBP safety, chemical inventory accuracy, training record completeness, CHP effectiveness, and incident analysis, you’ll ensure a safer environment for your staff and maintain compliance with OSHA standards.
Compliance Tool: Checklist for OSHA Review of Laboratory Health and Safety Program This checklist can help ensure you cover all the key elements of an annual OSHA review of your lab’s health and safety plan. Click the title above to download. |
Subscribe to view Essential
Start a Free Trial for immediate access to this article