Common OSHA Violations: What Could Go Wrong?
What lab safety violations are most common? What happens when lab safety is overlooked? And how can your lab avoid becoming a statistic?
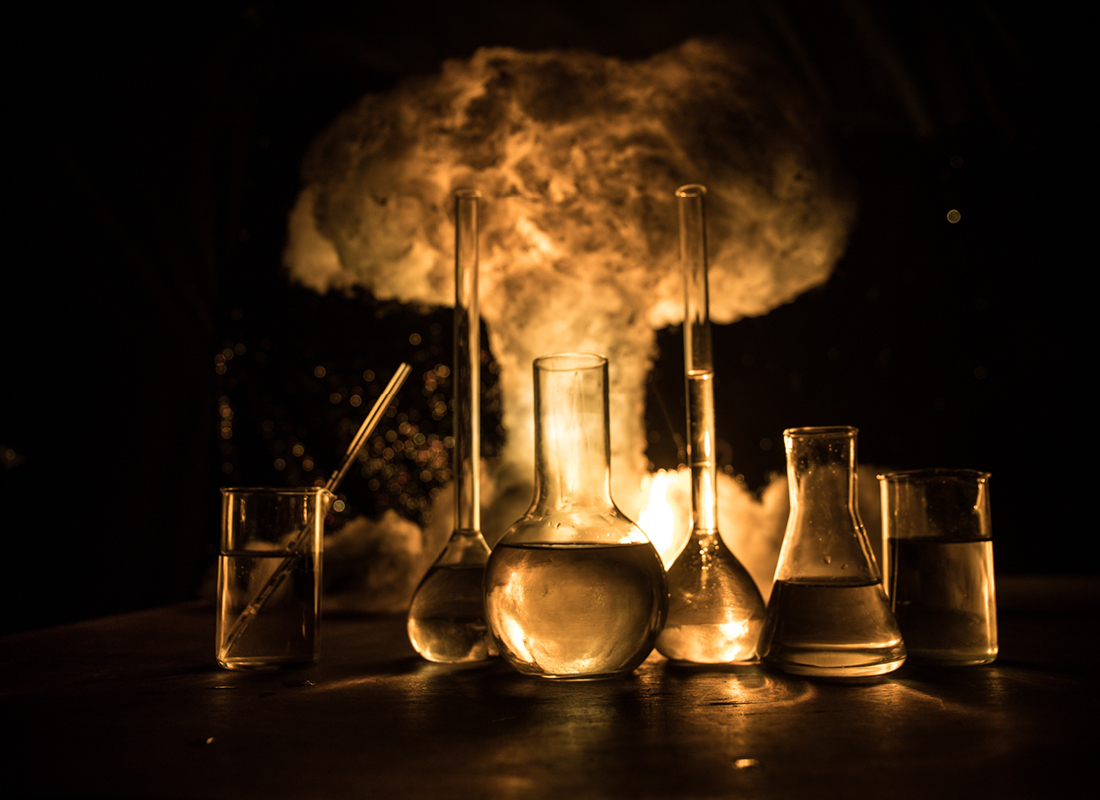
“Should I fire my employee?” were the first words of a phone call lab safety expert James Kaufman received. When asked what the employee had done, the reply was, “He took his chemical reaction from the lab to the lunchroom and ran it in the lunchroom microwave.”
Kaufman, who is founder and president emeritus of the Laboratory Safety Institute, says, “In the wildest stretch of my imagination, this isn’t something I would have imagined somebody would do”—but lab safety often involves anticipating the unforeseeable. In this case, Kaufman recommended against firing the employee and instead suggested signage and documentation to make it explicit that chemical reactions must only be performed in the laboratory.
“Often, the issue is that procedures aren’t adequately described in the safety documentation we provide,” he explains. “This is why it’s vital to have a good lab safety manual that covers all nine types of hazards—chemical, physical, biological, mechanical, noise, radiation, pressure, electrical, and stress—not only in the workplace, but off the job as well.”
“I was in a blood banking laboratory where they discarded all of their syringes into a cardboard box. The cardboard box was so full that it looked like a porcupine. There was no way to pick it up without impaling yourself!”* |
Safety shortfalls
Kaufman says the most common Occupational Safety and Health Administration (OSHA) violations he sees in the lab often relate to documentation.1 “When it comes to compliance with the laboratory standard, a major one is not having a Chemical Hygiene Plan,” he says.2,3 “Thirty years after this regulation went into effect, there are still people who don’t have a written plan. They don’t have the required chemical hygiene officer. They aren’t providing the required information and training—at the time of employment, whenever the nature of the hazards change, and as often thereafter as the employer feels is necessary.”
Another issue Kaufman frequently encounters is that the lab does have a plan—but it’s presented as guidance, rather than as “the rules and policies that one either must or should follow.” In the case of OSHA, must and should are legal terms with different meanings.4 Must means that the instruction in question is mandatory, whereas should means that it is preferable to alternatives, but leaves the final judgment up to the lab.
The final area Kaufman highlights is hazard determination. For everything from complex equipment to potentially infectious patient samples, OSHA requires documentation that a hazard assessment has been conducted. Chemicals that fall under the hazard communication standard must have a classification, safety data sheet, and label that includes both text and images. Additionally, employers are required to provide training on these safety data sheets and labels to ensure that their staff fully understand them.5 For personal protective equipment (PPE), the written certification must include the workplace that was evaluated, the date on which it was evaluated, and the person who conducted the evaluation.6
“It’s the employer’s responsibility to document that they have identified the hazards that are present in the workplace, selected the PPE that’s needed, made sure it’s available, and ensure that it is used,” says Kaufman. “But, when I teach lab safety, I find that most of my students have never seen such a document, nor do they know whether their organization even has it. So that’s an action idea—something they can go back to their labs and work on improving.”
“At a police forensic laboratory, I saw a person sitting at a bench. Next to them on the floor was a basket and they were dropping used blood samples to land—and splash—in this basket. That is not how blood samples are properly handled; somebody could become very sick.”* |
A top-down solution
To advance lab safety, it’s vital that lab and institutional leaders understand their critical role. “The central safety committee for a clinical lab should involve the chief executive officer, lab director, and anyone who reports directly to the lab director,” says Kaufman. “They should get together once a week—or more—to discuss how things are going from a safety perspective. We want these leaders to care more about safety, to be actively involved, and for that involvement to radiate downward.”
Engagement with safety starts as soon as new employees join the lab. Although many labs require staff to confirm that they have read the safety manual, understood it, and agree to follow it, Kaufman says they are missing a key component. “Read, understood, and agree to follow are good—but better still is realize,” he says. “Employees realize that, if they don’t follow the safety rules, they can face disciplinary action up to and including termination. In the absence of that step, your safety guidance is essentially just a nice idea.”
After onboarding, every staff member should have responsibilities that contribute to the lab’s overall safety plan. For individual contributors, this might involve overseeing a specific area of the lab, creating and maintaining documentation, or assisting with training for new employees. For senior management, it might include establishing and participating in regular laboratory inspections, identifying areas of concern and sourcing additional training, or requesting additional funding to enhance the lab’s existing safety program.
“Biosafety cabinets are common sources of safety issues. Sometimes there are UV lights in them and people don’t realize that the lights are on, so they stick their heads in and end up burning themselves. I had one client who had five sash cables break over three years and on the fifth incident the guy had his head in the hood. Most people don’t regularly check the integrity of the sash cables on their fume hoods and biosafety cabinets to make sure they aren’t going to break and drop a heavy glass-and-metal door on the user.”* |
“Lab safety is a marathon, not a sprint,” Kaufman concludes. “Never assume anything—and always remember four simple safety questions: what are the hazards? What can go wrong? What should you do if it goes wrong? And how can you minimize the risk?”
*All boxed quotes are from lab safety expert James Kaufman on extreme examples of common safety issues he has seen in laboratories.
References:
-
- Occupational Safety and Health Administration. Laboratories. https://www.osha.gov/laboratories.
- Occupational Safety and Health Administration. OSHA FactSheet: Laboratory Safety Chemical Hygiene Plan (CHP). August 2011. https://www.osha.gov/sites/default/files/publications/OSHAfactsheet-laboratory-safety-chemical-hygiene-plan.pdf.
- 29 CFR Part 1910.1450. Occupational exposure to hazardous chemicals in laboratories. Federal Register. October 9, 2024. https://www.ecfr.gov/current/title-29/subtitle-B/chapter-XVII/part-1910/subpart-Z/section-1910.1450.
- Paxton L. Should, Shall and Must. Safety First Blog. January 19, 2021. https://www.rpharmy.com/blog/should-shall-must-interpreted.
- Occupational Safety and Health Administration. Hazard Communication. https://www.osha.gov/hazcom.
- 29 CFR Part 1910.132. General requirements. Federal Register. October 9, 2024. https://www.ecfr.gov/current/title-29/part-1910/section-1910.132#p-1910.132(d)(2).
Subscribe to view Essential
Start a Free Trial for immediate access to this article